Why Should You Try Optimum Line Versatile Tools
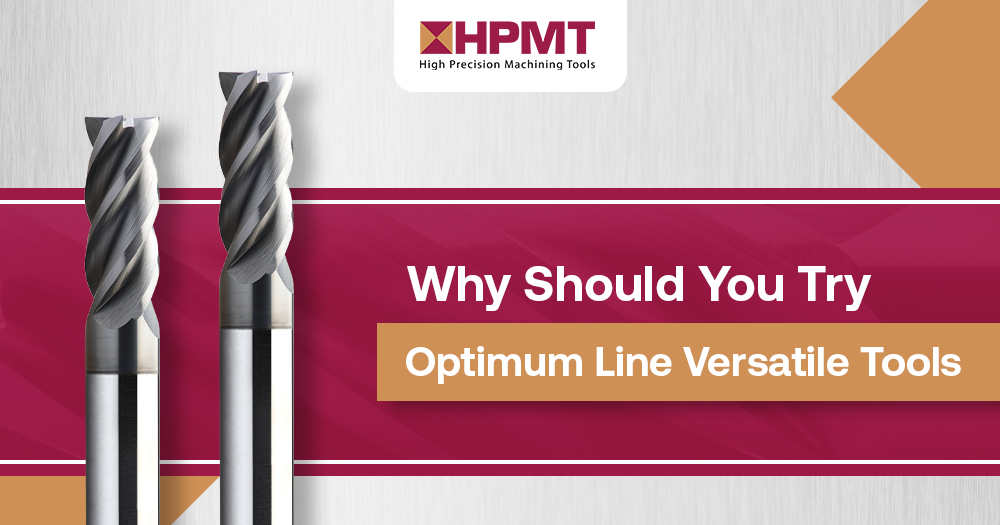
In the dynamic world of manufacturing, precision isn't just a preference; it's an absolute necessity. Every day, countless industries rely on the art of machining to transform raw materials into finely crafted components, intricate moulds, and meticulously engineered parts. At the heart of this transformative process lie high-quality tools, instrumental in realizing our client’s most ambitious designs.
It's the precision of every cut, every hole, and every shaping operation that ensures the finished product adheres to accurate specifications. High-quality tools epitomize this attention to detail, playing a vital role in achieving excellence. Quality and versatility are the twin pillars upon which these exceptional tools stand.
Let's explore why quality-driven and versatile tools are not just desirable but absolutely critical in the world of machining:
List of Services
-
1. Accuracy and Precision:List Item 1
High-quality tools are crafted with an unwavering commitment to detail. This meticulousness is essential for meeting the stringent tolerances that various industries demand, ensuring accurate and consistent results in machining.
-
2. Reduced Downtime:List Item 2
Versatile tools adapt effortlessly to a variety of materials and applications. This flexibility reduces the need for frequent tool changes, minimizing downtime, increasing productivity, and streamlining machining processes.
-
3. Cost-Efficiency:List Item 3
High-quality tools often boast extended tool life due to superior materials and coatings. This reduces the frequency of tool replacement, leading to cost savings and improved overall machining economics.
-
4. Enhanced Surface Finish:
Quality tools contribute to impeccable surface finishes, which are crucial in industries like automotive, aerospace, and medical devices where aesthetics and functionality are paramount.
-
5. Broad Material Compatibility:
Versatile tools can confidently tackle an array of materials, from metals to composites to plastics. This adaptability aligns with the diverse landscape of modern manufacturing.
-
6. Flexibility in Applications:
Versatile tools excel in various machining tasks, from drilling and milling to slotting and threading. This flexibility empowers our machining community to address a wide range of projects without the need for specialized tools.
-
7. Improved Operator Efficiency: Write a description for this list item and include information that will interest site visitors. For example, you may want to describe a team member's experience, what makes a product special, or a unique service that you offer.
-
8. Consistency and Quality Assurance:
Quality tools maintain unwavering consistency across production runs, guaranteeing that each component or part adheres to the exact specifications and standards set by our industry.
-
9. Customer Satisfaction: Write a description for this list item and include information that will interest site visitors. For example, you may want to describe a team member's experience, what makes a product special, or a unique service that you offer.
-
10. Environmental Benefits:
Quality tools contribute to sustainability by reducing waste, conserving energy, and optimizing machining processes.
HPMT Optimum Line: Precision meets versatility
When it comes to versatility, HPMT's best-selling Optimum Line reigns supreme as it offers the most versatile program for multiple materials and applications. This remarkable line of high-precision tools seamlessly adapts to various materials and applications, simplifying your machining processes and elevating your productivity to new heights.
Let’s take a look at the features and benefits of the Optimum Line:
- Differential Pitch (DP)
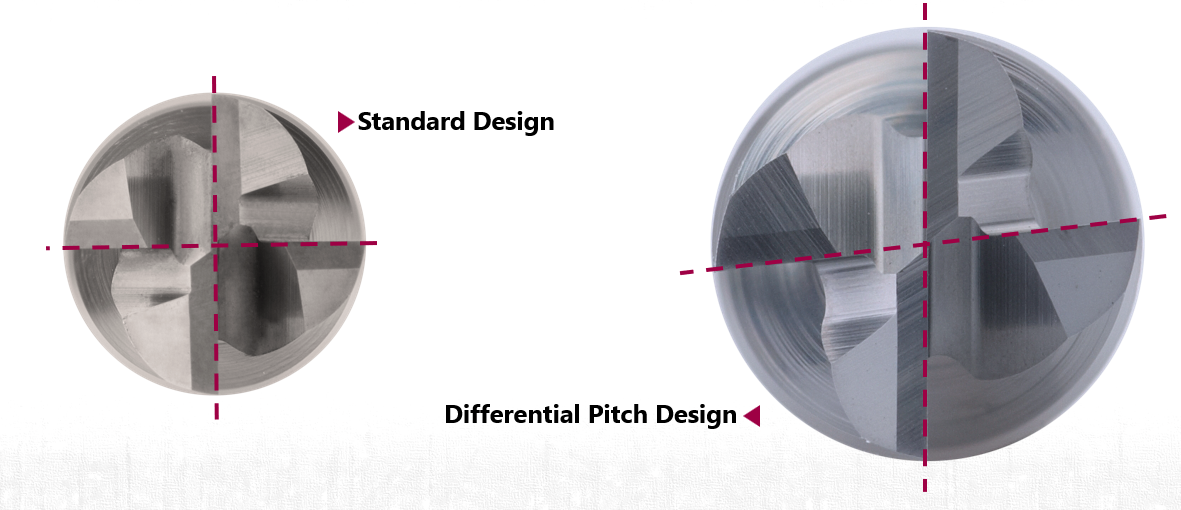
In machining, vibrations pose significant challenges. Optimum Line tools come with a Differential Pitch (DP) feature that combats this issue by reducing vibration. It ensures a smoother, more efficient machining process, resulting in heightened productivity and the finest quality finished products.
- Differential Helix (DH)
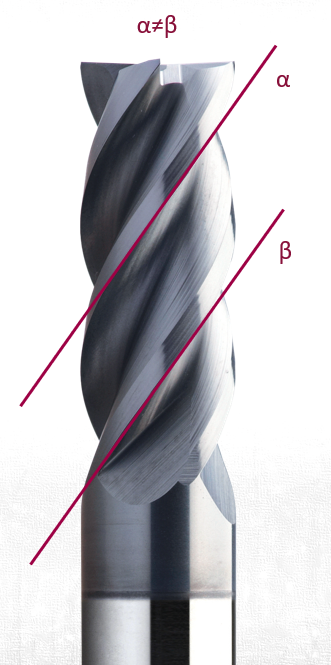
It tackles machining vibrations, enabling high-speed operations for heightened productivity. It ensures chatter-free machining, impeccable surface finishing, a smooth joining area and tighter accuracy on the radius, collectively elevating machining precision and efficiency.
- Ideal Cutting Edge
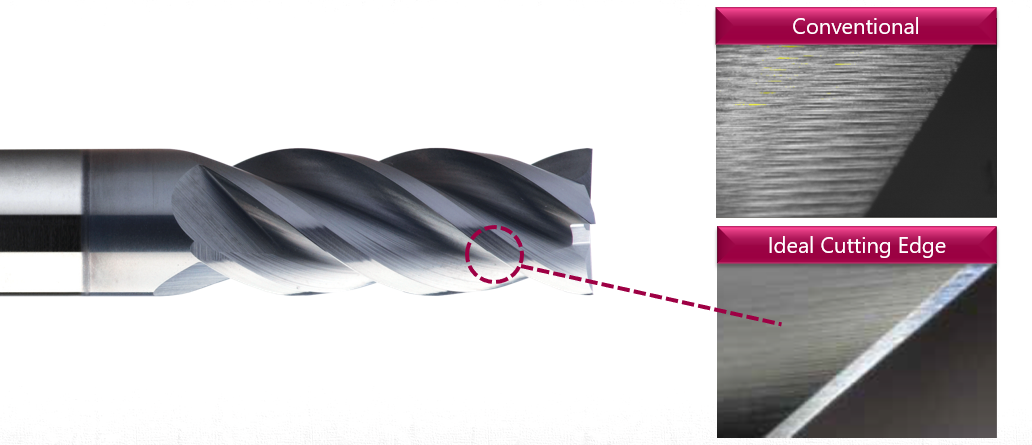
Optimum Line tools sport an ideal cutting edge that not only enhances durability but also acts as a guardian, preserving the tool's longevity. This translates to prolonged tool life and less frequent replacements, culminating in cost-effective and reliable machining.
- Superior Coating
The existence of heat can disrupt your machining operations. It accelerates tool wear and compromises performance. Optimum Line tools, equipped with superior coatings, are your defense against this formidable foe. These coatings enhance heat resistance, extend tool life, and minimize wear, making them synonymous with cost-effective and consistent machining.
Which Industries Optimum Line Would Work Best
The Optimum Line is designed to bring versatility in a single tool for those seeking a one-stop solution to today’s most common machining applications and materials. These versatile tools cater to a spectrum of industries, with a particular focus on general engineering and the mold and die sector.
For the general engineering sector, where quality and versatility are the lifeblood of operations, Optimum Line tools rise to the occasion. They adapt seamlessly to diverse materials and applications, streamlining operations and maximizing efficiency.
In the mold and die industry, Optimum Line tools excel in crafting intricate molds for automotive components, consumer electronics, and medical devices. They ensure your molds are nothing short of perfection.
Optimum Line is suitable for multiple materials:
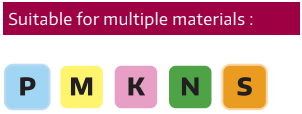
These are the multiple applications that Optimum Line can be used for:
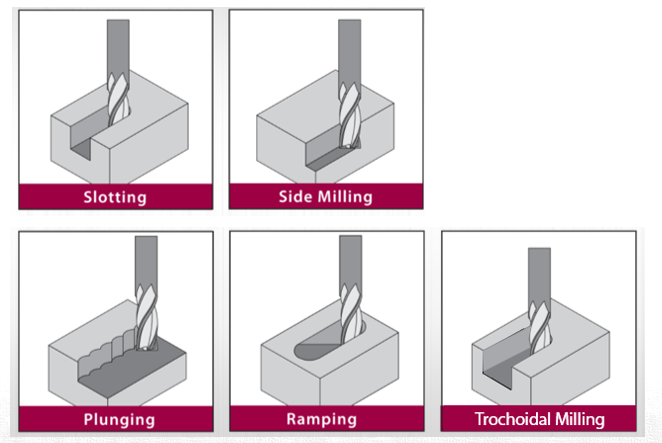
In the world of machining, accuracy reigns supreme, and the demand for quality and versatile tools has never been greater. HPMT's Optimum Line emerges as the answer, seamlessly blending accuracy with unparalleled versatility and cost-efficiency. Whether you're crafting aerospace components or automotive moulds, Optimum Line stands as the vanguard of exact machining.
Why should you try Optimum Line? Because they are not just tools; it's a commitment to excellence. These high-quality tools reduce vibrations, ensure chatter-free machining, and deliver impeccable surface finishes. Ideal for industries like general engineering and mould and die, they adapt effortlessly to various materials and applications. With Optimum Line, you're not just investing in tools; you're investing in accuracy, efficiency, and the assurance that your machining endeavors will rise above the competition.
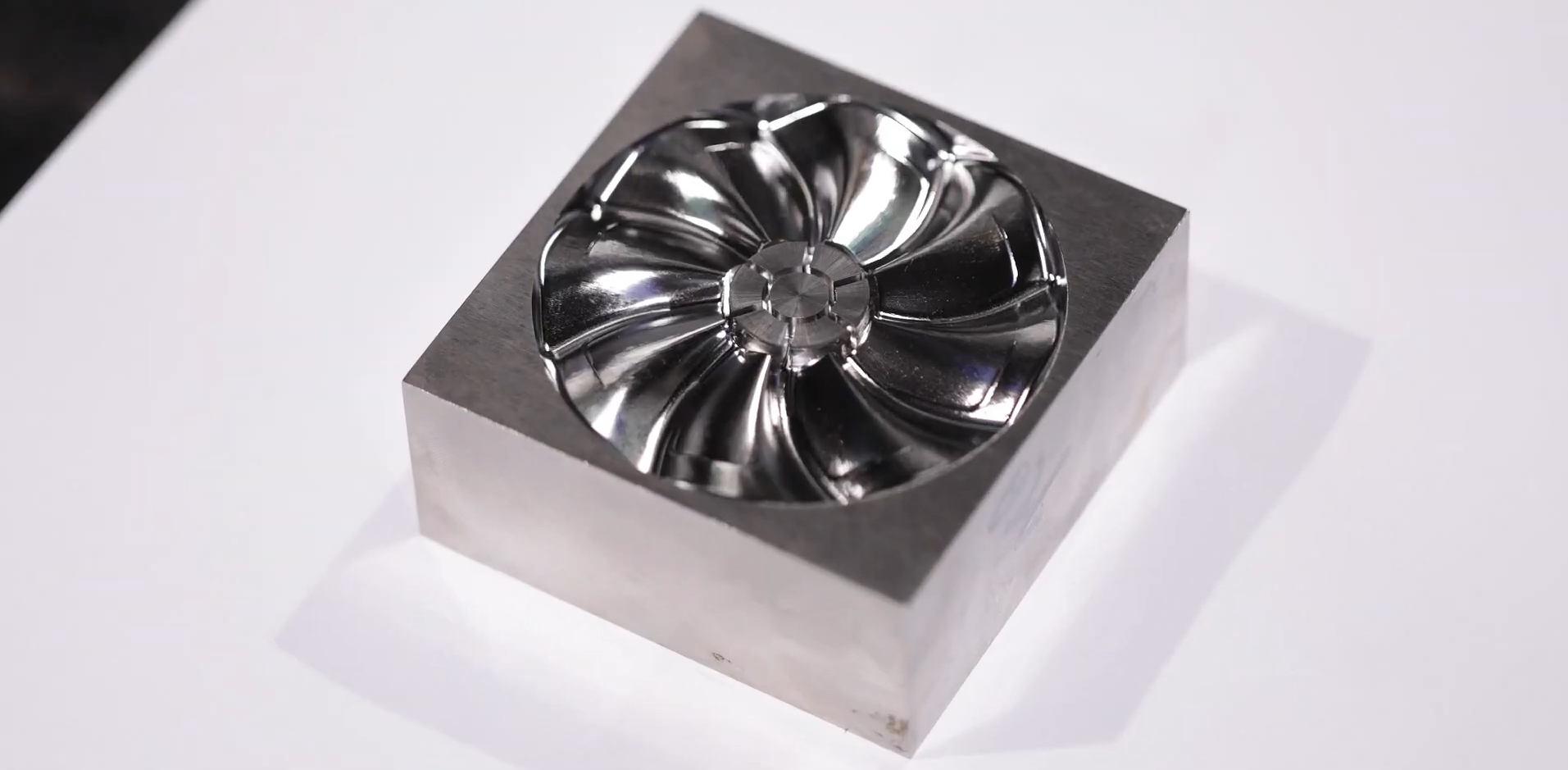
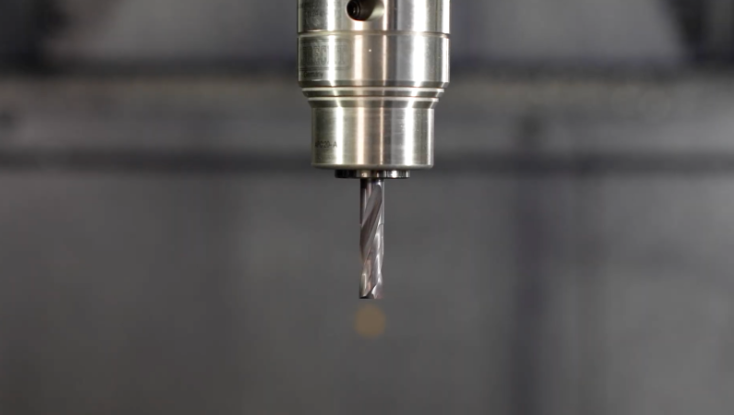
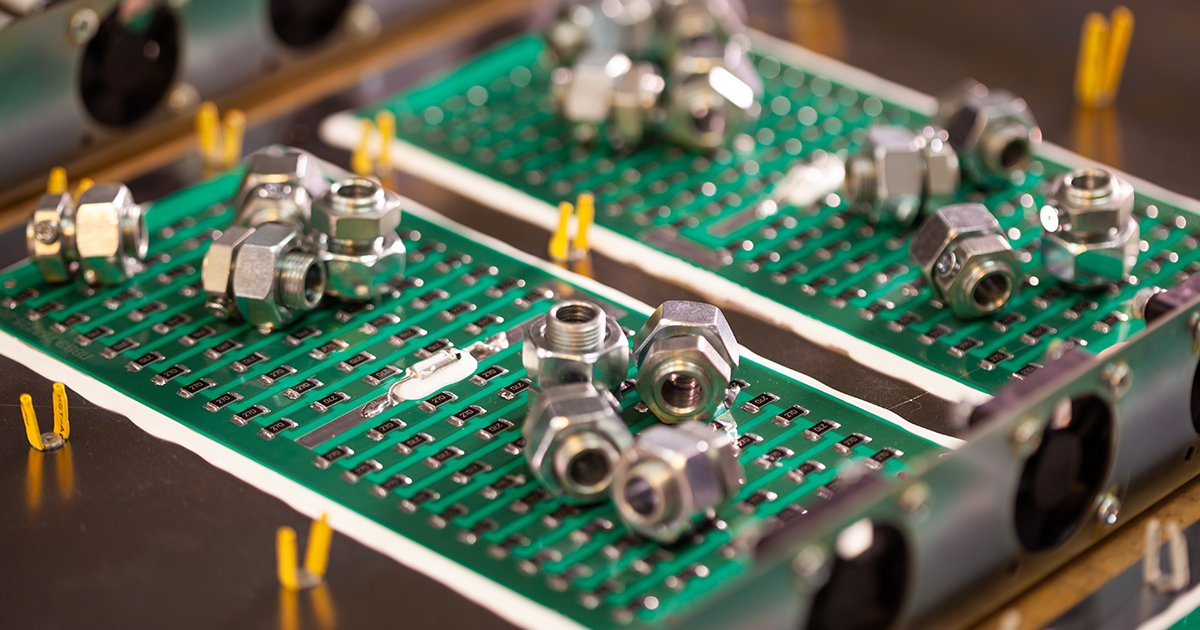
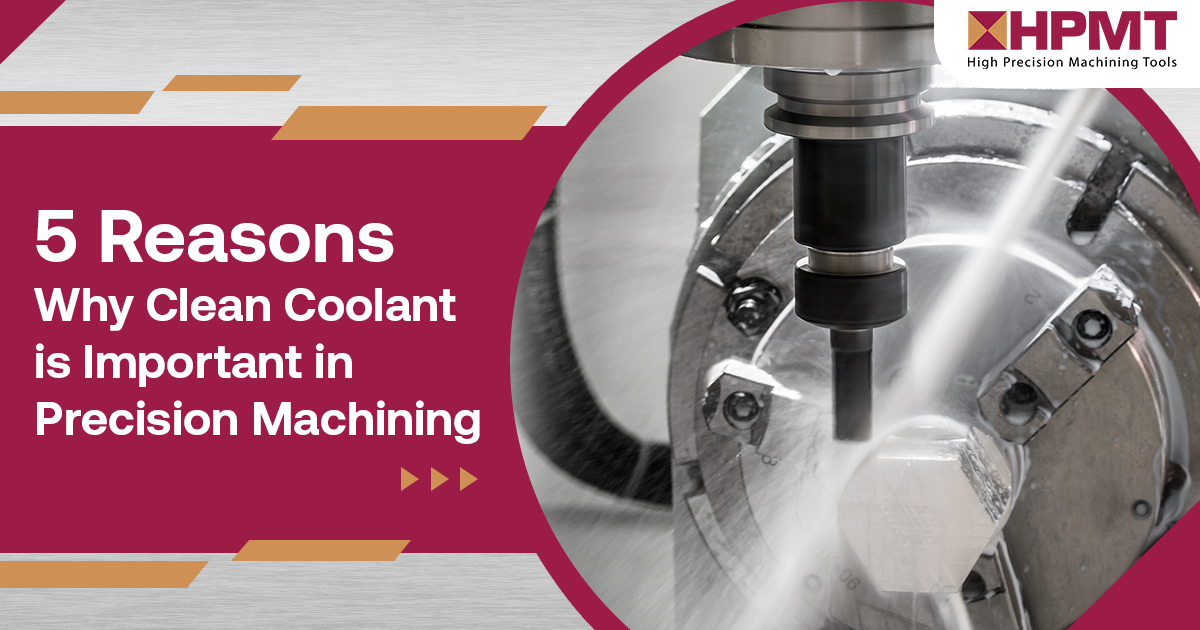
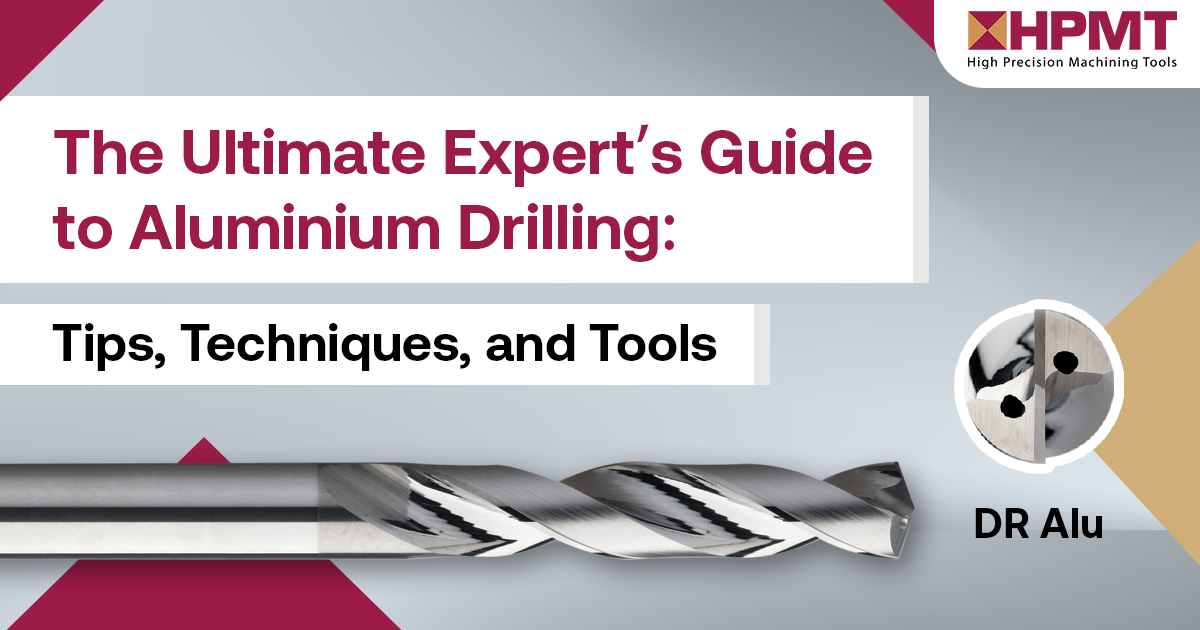