How to Achieve Precise Deep Hole Drilling with Long Drills
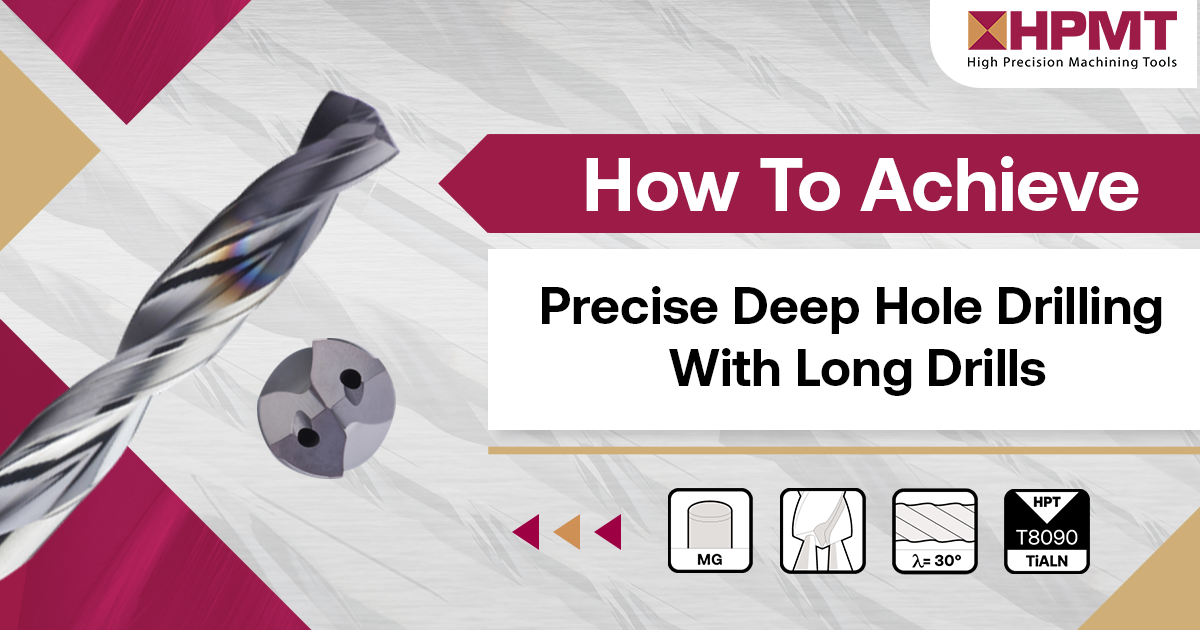
Deep hole drilling is a specialized machining process that involves creating holes with a high depth-to-diameter ratio. These holes are typically considered "deep" when they are at least ten times their diameter in depth. Deep hole drilling is essential in various industries, including aerospace, automotive, medical, and mold manufacturing. Achieving precise results in deep hole drilling, especially with long drills, is crucial for the quality and functionality of the final products.
In this article, we will explore what deep hole drilling is, the process, its applications, the challenges it presents, and how to achieve precise deep hole drilling with long drills.
What Is Deep Hole Drilling?
Deep hole drilling is a machining process used to create holes with an extended depth. These holes are typically required for specific applications, such as oil and gas exploration, firearm barrels, hydraulic cylinders, and cooling system components. The process involves removing material to create a hole, and it is characterized by its high depth-to-diameter ratio.
Applications of Deep Hole Drills
Deep hole drilling finds applications in various industries. Some common uses include:
- Aerospace: Deep hole drilling is essential for aircraft components, such as landing gear struts and turbine engine components.
- Automotive: The automotive industry relies on deep hole drilling for the production of engine blocks, drive shafts, and fuel injectors.
- Medical: Surgical instruments and medical implants often require deep, precise holes, and deep hole drilling ensures these critical components meet quality standards.
- Mold and Die Manufacturing:
The mold and die industry uses deep hole drilling to create precise cooling channels in molds for plastic injection or die-casting.
The Process of Deep Hole Drilling
Deep hole drilling is typically done using specialized tools, such as gun drills or BTA (Boring and Trepanning Association) drills. The process generally consists of the following steps:
- Drilling: The initial hole is created using a drill, which is often followed by a reaming or boring operation for size control and surface finish improvement.
- Coolant and Chip Evacuation: Deep hole drilling generates a substantial amount of heat, so a high-pressure coolant system is used to reduce temperature and lubricate the cutting tool. Efficient chip evacuation is crucial for process stability.
- Quality Control: Ongoing quality checks are essential to ensure the hole's diameter, straightness, and surface finish meet the required specifications.
Challenges of Deep Hole Drills
Deep hole drilling presents unique challenges, such as:
- Chip Control: Efficient chip evacuation is crucial to prevent chip accumulation, which can lead to tool breakage or poor surface finish.
- Straightness: Maintaining hole straightness over extended depths can be difficult.
- Size Control: Controlling the hole's diameter, roundness, and surface finish can be challenging.
- Heat Generation: The process generates heat, which can cause tool wear and affect material properties.
How to Achieve Precise Deep Hole Drilling with Long Drills
To achieve precise deep hole drilling, especially with long drills, the following can be considered:
- Tool Selection: Choose the appropriate drill type for your application, such as gun drills for high precision.
- High-Pressure Coolant: Implement an efficient high-pressure coolant system to reduce heat and assist in chip evacuation.
- Tool Alignment: Ensure precise tool alignment to maintain hole straightness.
- Quality Control: Regularly inspect and measure the hole's diameter, straightness, and surface finish.
- Feed and Speed Optimization: Adjust feed rates and cutting speeds based on material and hole depth.
Deep hole drilling is a critical process in various industries, demanding high precision and reliability. By understanding the process, its challenges, and following best practices, it is possible to achieve precise deep hole drilling with long drills. Selecting the right tools, optimizing cutting parameters, and implementing efficient coolant systems are key steps in ensuring the quality and accuracy of deep holes.
In this context,
HPMT's DR-LX deep hole twist drills offer a cutting-edge solution designed for flexibility and precision, making them an ideal choice to meet your deep hole drilling needs. Whether you're in aerospace, automotive, medical, or mold manufacturing, the ability to achieve precise deep hole drilling is essential for meeting stringent quality requirements and producing components that perform flawlessly.
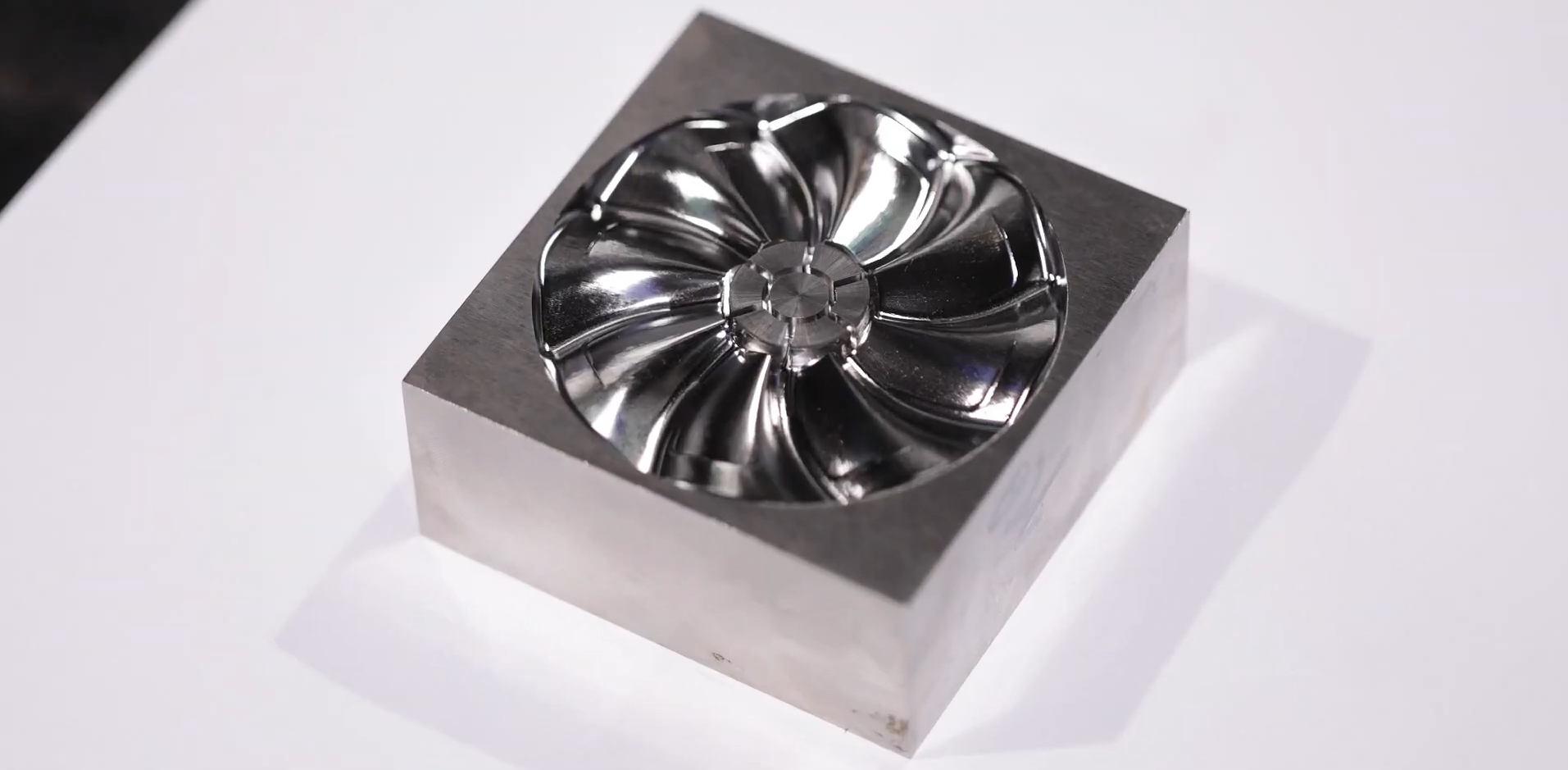
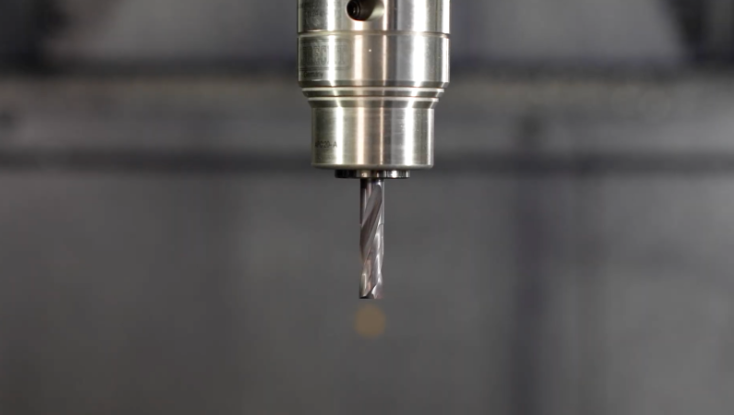
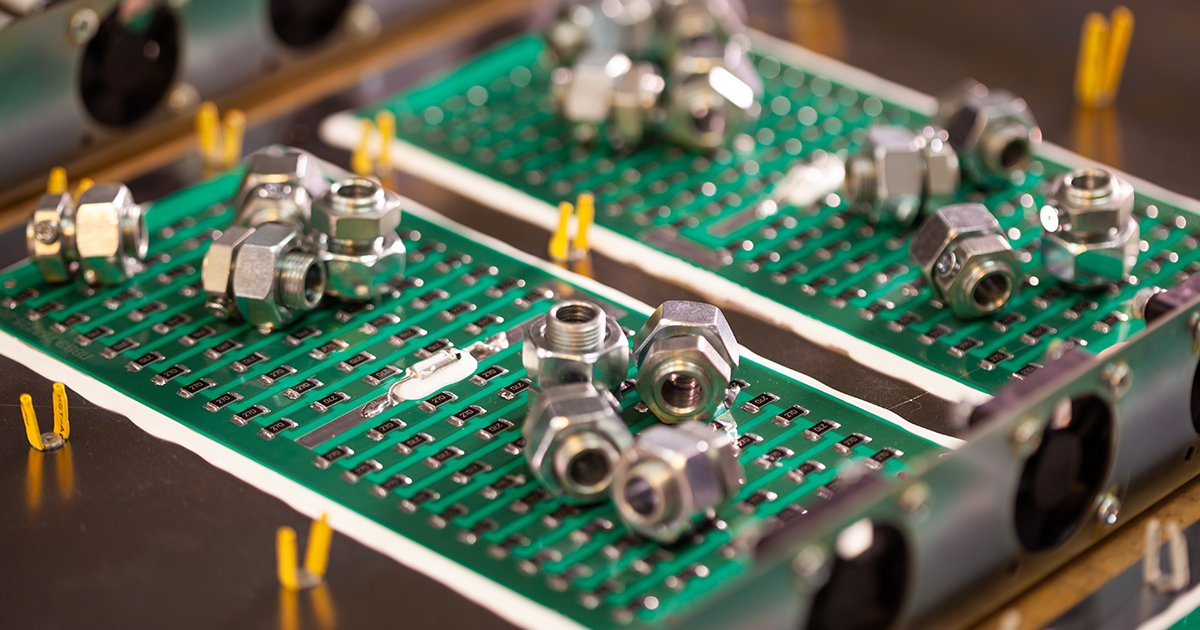
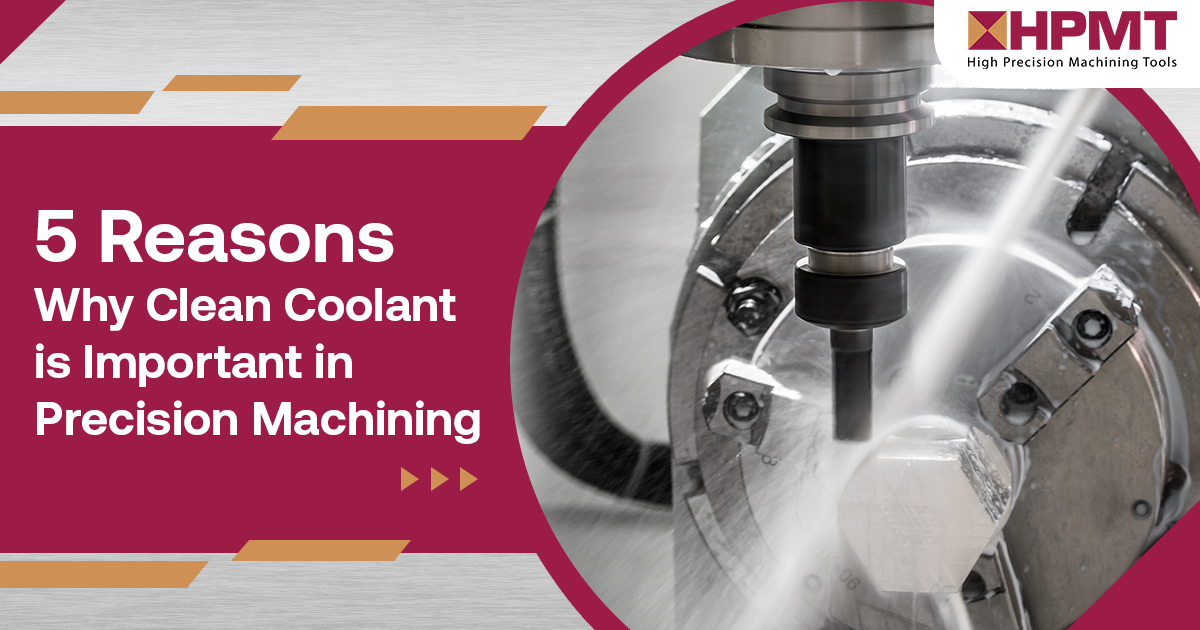
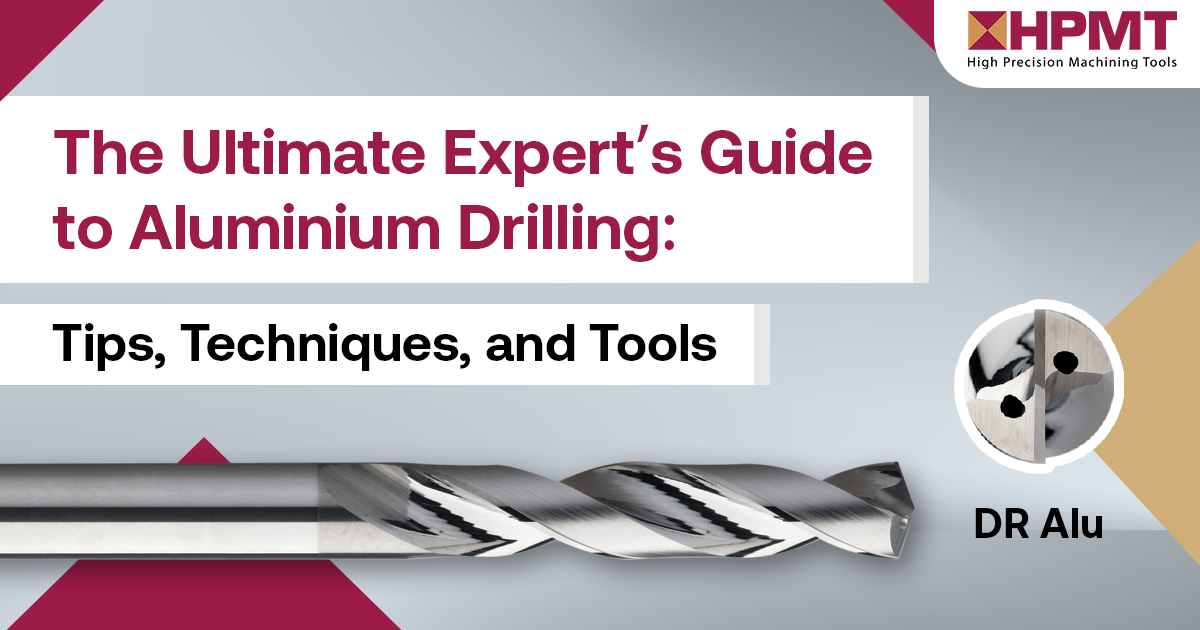