DM70X Series: Tackling 70 HRC Hardened Steel with Confidence
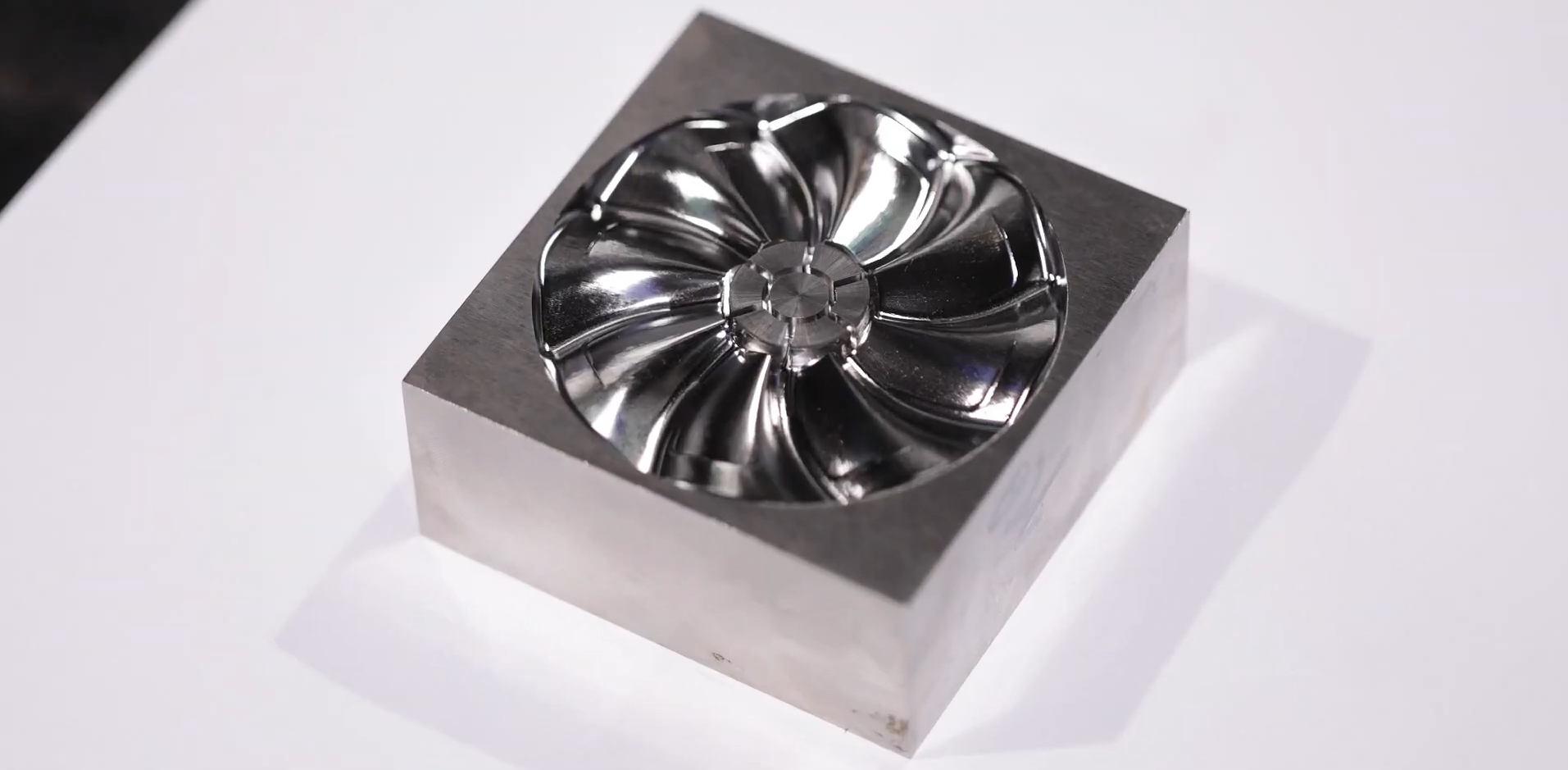
In Die & Mold machining, hardened materials are both a necessity and a challenge. Steels with hardness levels between 50 and 70 HRC push cutting tools to their limits, generating heat, wear, and unpredictable outcomes. If your tools can’t keep up, you lose more than productivity — you lose precision, surface quality, and profit.
That’s exactly why HPMT developed the DM70X series: a high-performance solution purpose-built to withstand extreme hardness and maintain dimensional integrity under pressure.
The Problem with Hardened Steel
Machining hardened steel isn't just tough on tools—it’s a constant trade-off between productivity and tool life. The heat, vibration, and edge wear that come with cutting 50+ HRC materials lead to:
- Premature tool failure
- Poor surface quality that demands secondary polishing
- Increased tool deflection and dimensional inconsistency
- Higher tooling and setup costs
This is where conventional tools fall short — struggling with accelerated wear, unstable performance, and inconsistent surface quality in hardened steel. DM70X overcomes these challenges with precision-engineered features and advanced coating technology, setting a new benchmark for reliability, tool life, and finish in Die & Mold applications.
What Makes DM70X Different
When it comes to machining hardened materials, not all tools are created equal. And the difference between an average result and a reliable one often comes down to the tool’s ability to maintain edge integrity, control heat, and deliver consistency across operations. DM70X was developed with these priorities at its core. From its advanced coating system to its precision-ground geometries, every element is engineered to solve the real-world challenges faced in Die & Mold applications. Below are the core capabilities that set DM70X apart in this demanding field.
1. New B0909X Coating with Higher Silicon Content
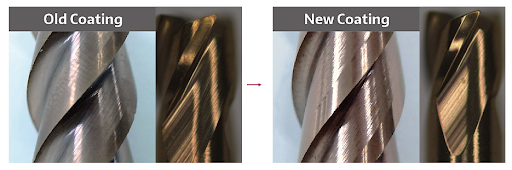
DM70X features an advanced B0909X coating formulated for high heat resistance and long wear life. Its enhanced silicon content improves surface adhesion, delivering a smoother finish and better chip evacuation. The result? A tool that runs cooler, cuts longer, and stays sharper.
2. Differential Pitch Geometry
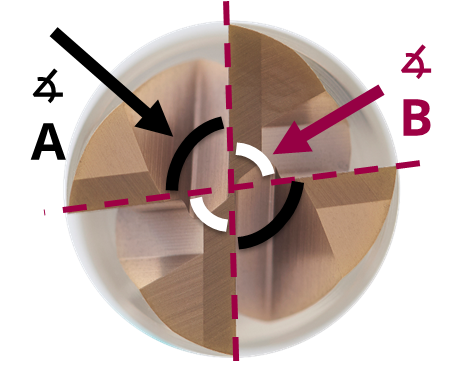
Unequal flute spacing significantly reduces vibration and chatter. This design delivers more stable cutting, which translates to superior surface finish and longer tool life.
3. Optimised Cutting Edge with Supreme Edge Technology
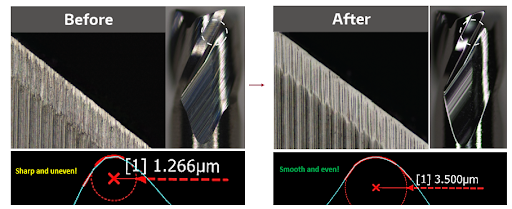
DM70X’s edge preparation is second to none. Smoother, more uniform edges reduce cutting resistance and ensure predictable behavior in high-hardness materials — resulting in Ra values as low as 0.160 µm.
4. Enhanced Dish Angle & Back Taper Optimization
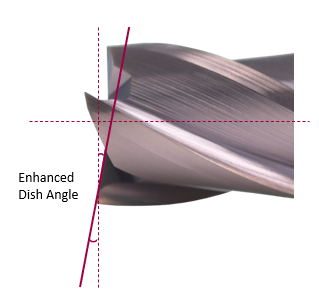
Precision design features such as an enhanced dish angle and back taper optimization (for < ⌀ 4mm tools) reduce tool deflection and avoid contact in deep cavities, ensuring better dimensional accuracy and finish.
5. Optimised Chisel Angle
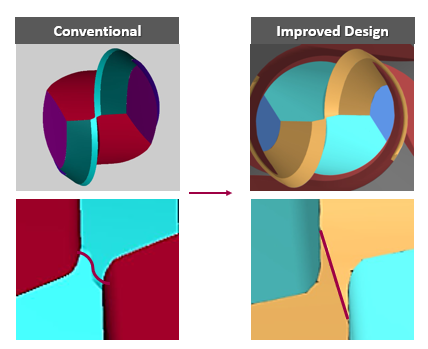
Delivers smoother entry, improved wear on the cutting face, and stability during high-speed passes. This supports tight tolerances in both semi-finishing and finishing applications.
Real Results That Engineers Like You Will Appreciate
Up to 3× longer tool life compared to conventional endmills in hardened steel
DM70X tools are built with B0909X coating, offering exceptional thermal and wear resistance—even when cutting materials in the 50–70 HRC range. This allows the tool to retain edge sharpness under prolonged high-load conditions, which is often where conventional tools fail due to micro-chipping or thermal fatigue. In demanding Die & Mold environments where machining hours are long and part complexity is high, the ability to complete full jobs without mid-cycle tool changes directly improves tool efficiency and shop-floor productivity.
Less polishing due to cleaner surface finishes
Surface integrity is critical in Die & Mold manufacturing, especially when parts must meet strict aesthetic or functional tolerances. The Supreme Edge Technology used in DM70X ensures uniform cutting edge quality, while differential pitch and optimised chisel angles promote controlled chip formation and reduced cutting force variation. This results in better as-machined surface roughness—often in the sub-micron Ra range—minimising the need for manual polishing and reducing human error during post-processing.
Improved process stability across roughing, semi-finishing, and finishing
Engineers often face fluctuating cutting forces and vibration when transitioning between machining stages—particularly in hardened steel. DM70X mitigates these challenges with an optimised flute design and variable pitch architecture, which collectively dampen harmonic resonance and ensure smoother chip evacuation. This geometric stability, combined with high-performance coating adhesion, allows the tool to maintain predictable behaviour across different operations—helping maintain machine-tool synergy and reducing variability in cycle outcomes.
Consistent part accuracy with fewer tool changes and setup interruptions
Maintaining tolerance in complex features—such as deep cavities, thin walls, or sharp transitions—depends on a tool’s rigidity and its ability to resist deflection. DM70X incorporates design enhancements like back taper optimisation (particularly in <Ø4 mm micro tools) and a finely tuned dish angle, which reduce side loading and preserve axial stability. The result is reduced deviation over long tool paths, fewer adjustments during setup, and a higher degree of repeatability, especially in automated or unmanned machining environments.
Tooling Coverage for Every Stage
Whether you're roughing out tool steel, semi-finishing large surface areas, contouring precise geometries, or navigating deep and narrow cavities in hardened materials, DM70X offers the right tool for every stage of Die & Mold machining, ensuring consistent performance from first cut to final pass:
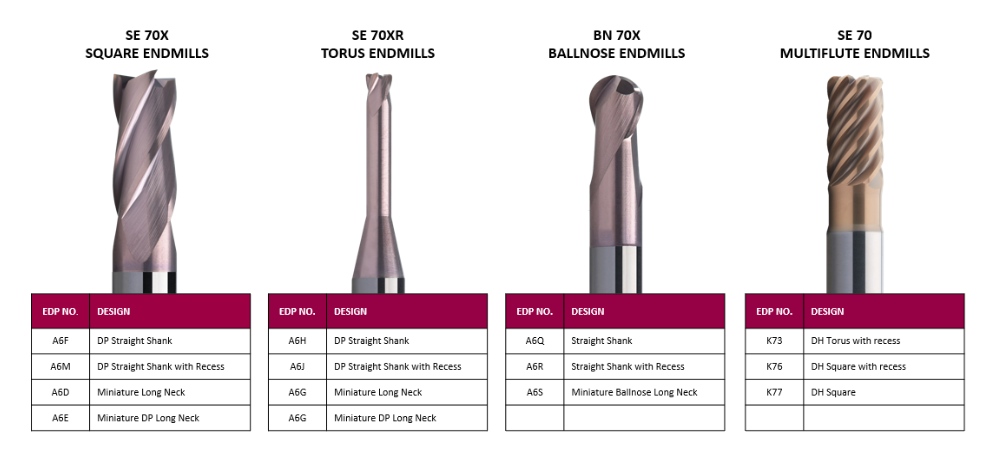
Each design is engineered for performance under pressure, delivering extended tool life and improved cut quality without sacrificing speed.
Takeaway for Engineers
If you’re machining 50–70 HRC materials, you don’t need a general-purpose cutter. You need a tool designed for the task. DM70X combines advanced coating, refined geometry, and proven durability to help you push productivity without compromising on quality.
Less polishing. Fewer tool changes. More control.
DM70X is how engineers take back the upper hand in hardened steel machining. Watch our tool test video below and see it for yourself.
Get more out of every cut with DM70X. Access the tool test results here.
At HPMT, our mission is simple: to empower manufacturers with tools that deliver results.
Contact us today to explore the full DM70X lineup or speak to our technical team to find the right tool for your application.
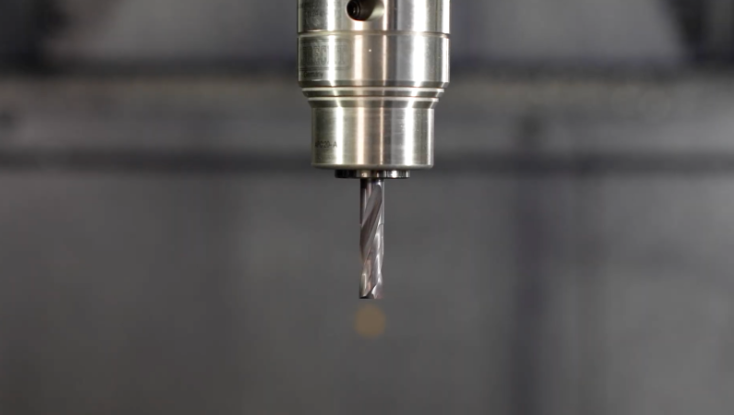
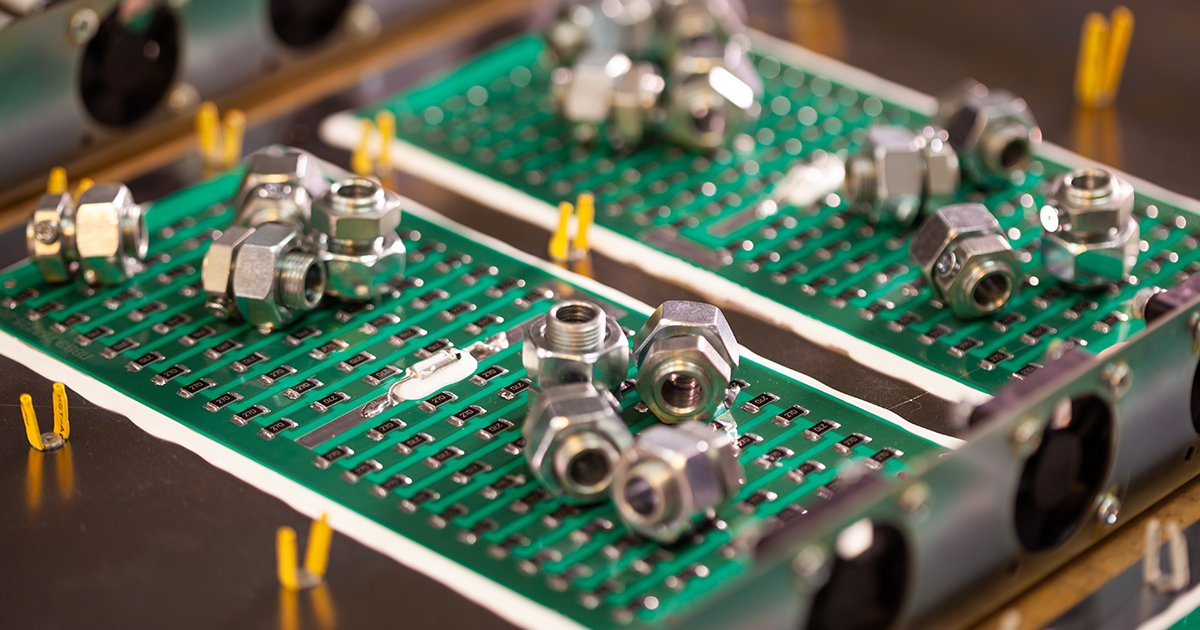
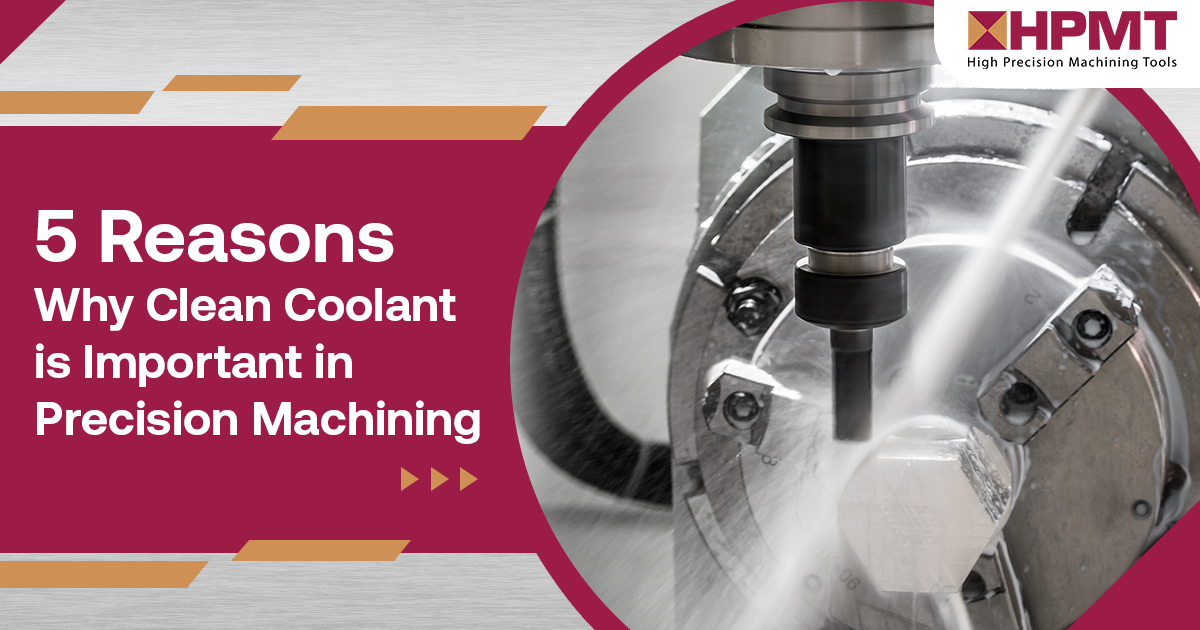
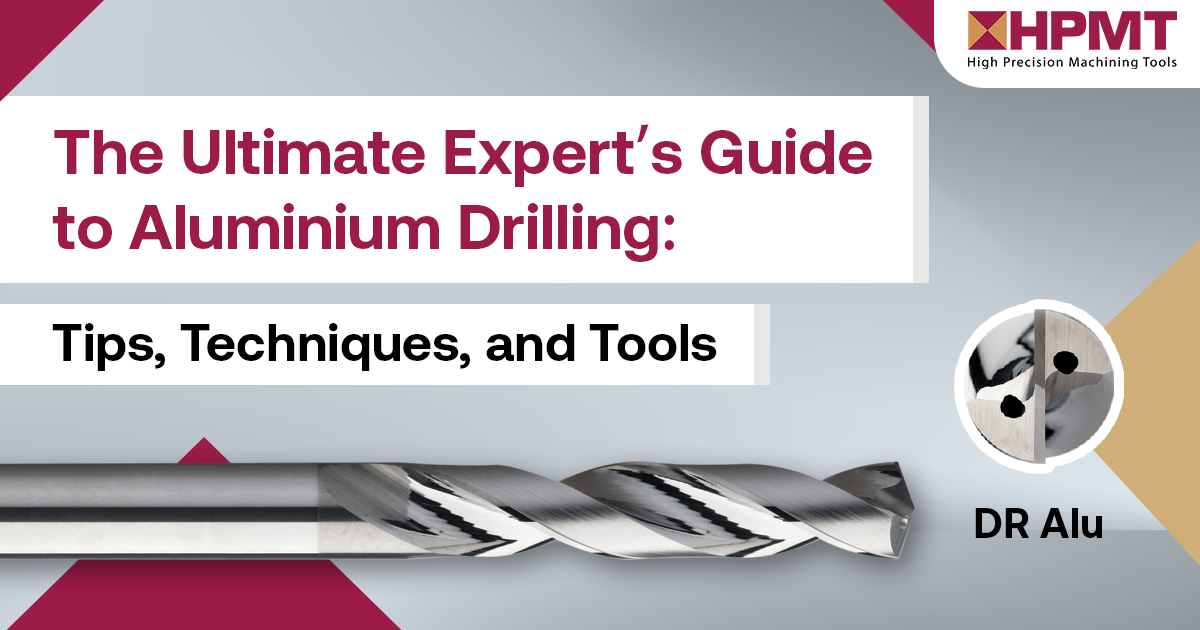
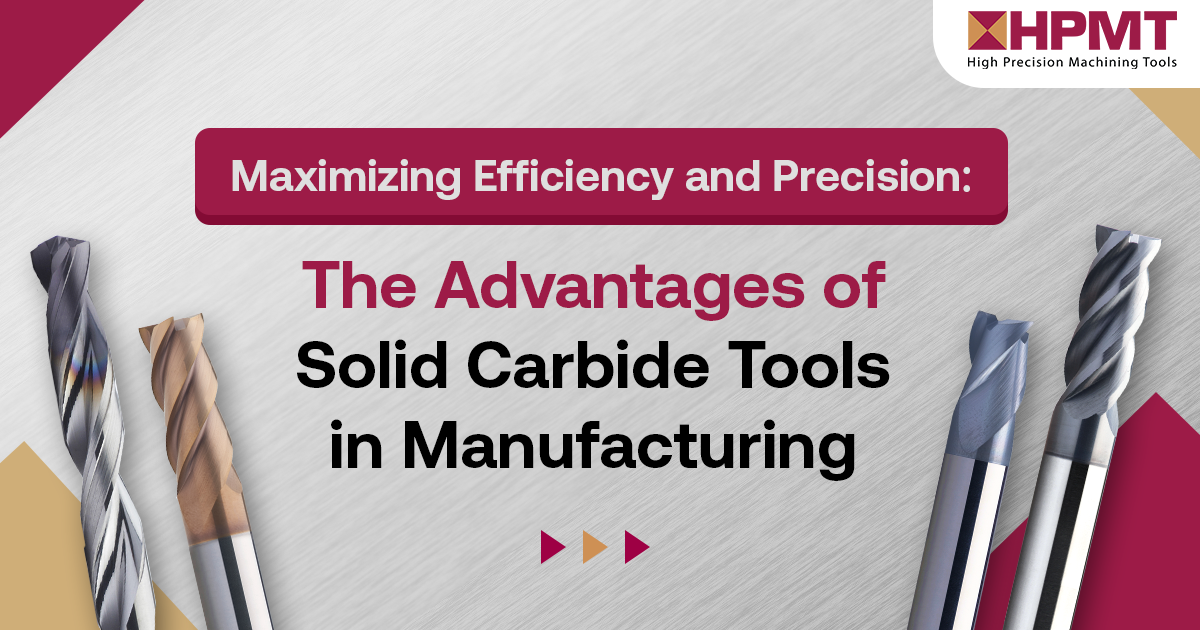