Tips to Choose the Perfect Helix Angle: The Key to Optimal Machining Efficiency
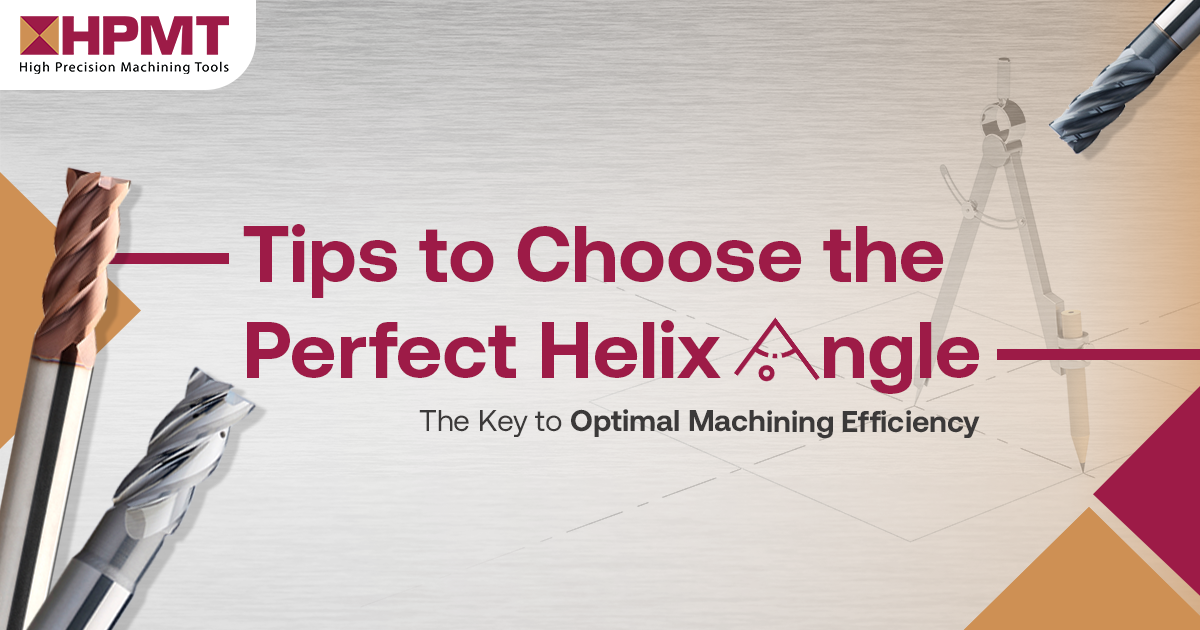
Discover the key factors behind choosing the perfect helix angle to elevate your machining projects. When machining, selecting the right tools and parameters is crucial for achieving optimal results.
One often overlooked aspect of machining is the helix angle of the cutting tool. The helix angle plays a significant role in chip evacuation, tool life, and overall cutting performance. In this comprehensive guide, we will detail the key points to consider when selecting the optimal helix angle for your machining needs.
Helix Angles - Rule of Thumb
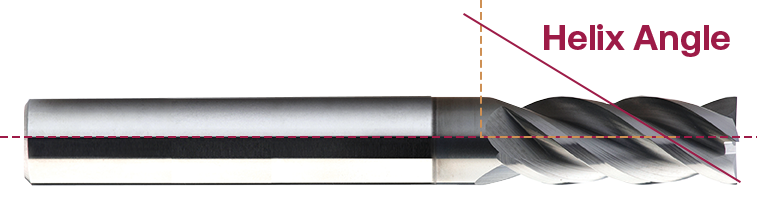
Generally, a helix is a seamless three-dimensional curve. This 3-D curve wraps itself in a spiral fashion around a straight axis. To grasp this concept easily, one can envision a helical spring, where the coils form the shape of a helix.
The helix angle refers to the angle formed between the cutting edge of a tool and a plane perpendicular to the axis of rotation. It affects chip evacuation, tool life, and cutting performance. A general guideline to keep in mind is that when the helix angle increases, the length of contact along the cutting edge will decrease.
The cutting edge refers to the sharp, leading edge of the helix, responsible for removing material from the workpiece as the tool rotates or moves along its cutting path. The higher helix angles benefit softer materials, while lower helix angles are preferred for tougher materials.
Difference between High and Low Helix Angles
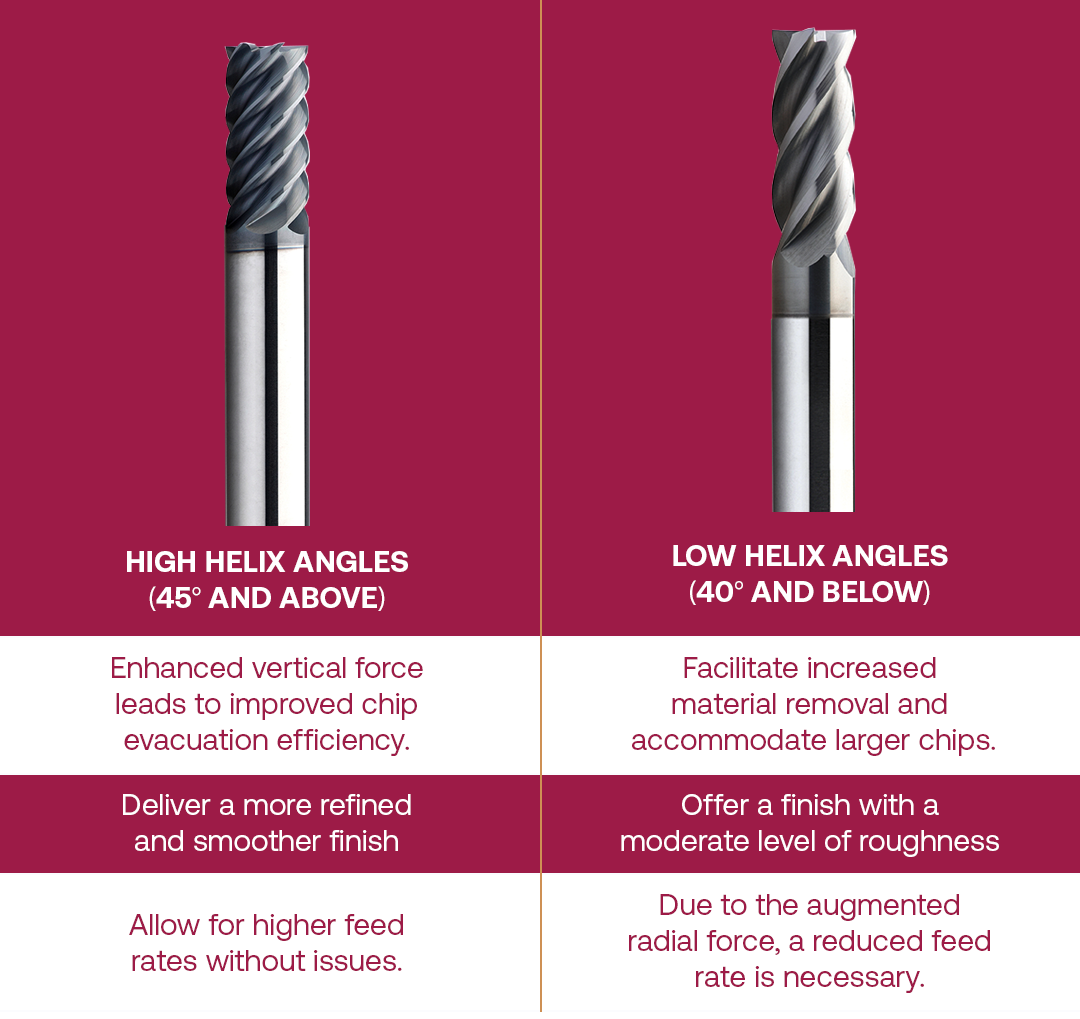
Note: The feed rate determines how fast the helix removes the material and how much force is applied to the tool and workpiece.
Advantages of High Helix Angles
List of Services
-
- Efficient chip evacuation:List Item 1
High helix angles promote effective chip removal, preventing chip clogging or re-cutting. They are advantageous for operations involving deep pockets, slots, or plunge milling.
The improved chip evacuation helps maintain consistent cutting performance and reduces the chances of tool damage.
-
- Reduced cutting forces:List Item 2
High helix angles result in lower cutting forces, reducing tool wear and minimizing the risk of workpiece distortion or deflection.
The reduced cutting forces also increase feed rates, improving productivity and reducing machining time.
-
- Improved surface finish:List Item 3
High helix angles minimize tool deflection and vibration, resulting in smoother surface finishes. This is particularly important when machining materials for which surface finish is a critical factor.
For instance, it applies to components that require cosmetic appeal or the parts that will undergo subsequent processes like painting or coating.
Disadvantages of High Helix Angles
List of Services
-
- Increased heat generation:List Item 1
High helix angles can lead to higher heat generation due to increased cutting forces. This may result in accelerated tool wear and compromise machining accuracy.
It is crucial to monitor and control temperatures during machining operations to avoid thermal damage to the workpiece or the tool.
-
- Reduced tool life:List Item 2
Higher heat generation and increased cutting forces may decrease tool life, especially when machining harder materials or engaging in heavy-duty cutting operations.
Proper selection of cutting speed, feed rate, and coolant application is crucial to mitigate the adverse effects of high helix angles on tool life.
Advantages of Low Helix Angles
List of Services
-
- Greater tool stability:List Item 1
Low helix angles provide greater rigidity, reducing the risk of tool deflection and vibration. This is particularly beneficial for machining operations that require higher cutting forces or involve tougher materials.
The increased stability allows for more aggressive cutting conditions, improving productivity.
-
- Longer tool life:List Item 2
The lower cutting forces associated with low helix angles often result in extended tool life, making them suitable for applications prioritizing tool longevity.
The reduced contact between the chip and the tool reduces wear, contributing to longer tool life and decreased tool changeovers.
Disadvantages of Low Helix Angles
Helix Angles Overview and Example
To further understand the impact of helix angles on machining outcomes, let's consider some specific examples:
List of Services
-
- A milling operation on aluminum:List Item 1
For machining softer materials like aluminum, a high helix angle (between 45° and 60°) would help ensure efficient chip evacuation and prevent workpiece deformation due to heat generation.
The softness of aluminum allows for effective chip flow, making it crucial to have a high helix angle to prevent chip recutting and improve surface finish.
-
- A milling operation on steel:List Item 2
When machining tougher materials like steel, a lower helix angle (between 20° and 30°) would provide greater stability, minimize cutting forces, and enhance tool life.
In the case of steel, the lower helix angle helps reduce chip clogging and allows for more stable cutting conditions, providing optimal tool performance.
It is important to note that these angles serve as general guidelines, and the optimal helix angle may vary depending on specific material properties, tooling, and machining conditions.
It's important to
consult our experts and
HPMT manufacturer's recommendations to select the optimal helix angle tailored to specific machining needs.
How to Choose the Right Helix Angles
List of Services
-
1) Meeting Productivity Needs:List Item 1
To achieve rapid material removal, a lower helix angle is preferred. Compensatory strategies, like using high helix tools for finishing and low helix for rough cuts, can mitigate the drawbacks.
-
2) Efficient Pocketing:List Item 2
Effective chip management is crucial in pocketing tasks. Opting for a high helix angle enhances chip evacuation, preventing adverse effects on tools and part quality.
-
3) Dealing with Thin Walls/Floors:
Thin walls and floors are prone to deformation from cutting forces. The helix angle directly influences these forces. Therefore, use a high helix angle tool to minimize radial forces and achieve fine finishes.
-
4) Balancing Tool Life:
The cutting edge of a high helix reduces cutter core strength, affecting tool life. Low helix also poses issues like heat accumulation and poor chip evacuation, impacting tool performance. Careful consideration is necessary for optimal tool life.
If you're looking for a cutting tool to address a wide range of machining applications and materials,
HPMT Optimum Line is designed to bring versatility to cater all your needs.
Conclusion
By understanding the role of helix angles in chip evacuation, tool life, and overall cutting performance, machinists can make well-informed decisions that result in successful and efficient machining outcomes. Choosing the right helix angle can significantly impact chip flow, tool life, and surface finish, ultimately improving productivity and cost-effectiveness in machining operations.
HPMT is committed to providing high-quality cutting tools and services to distributors worldwide.
Contact us today to learn more about
our products and services.
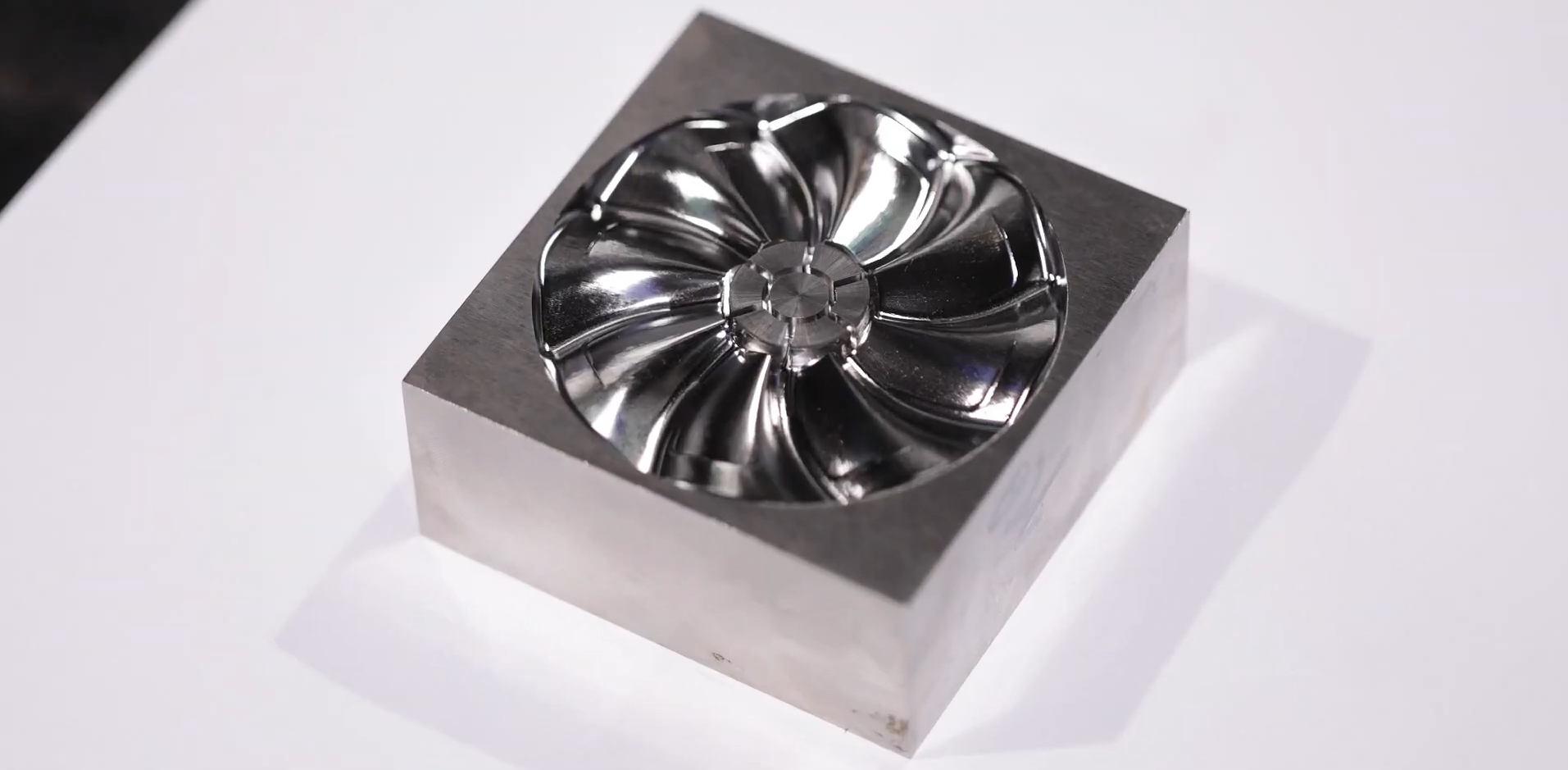
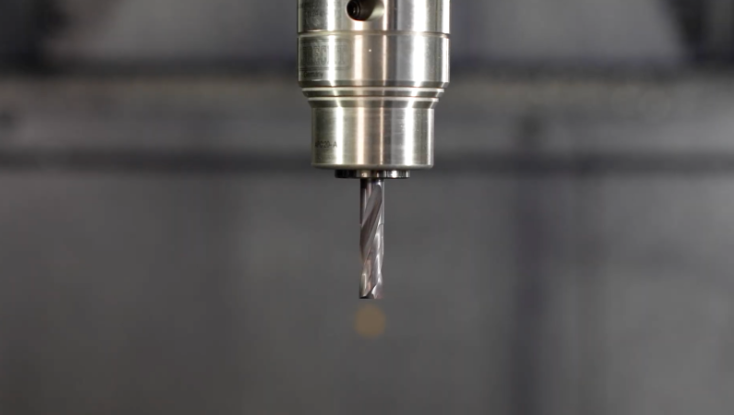
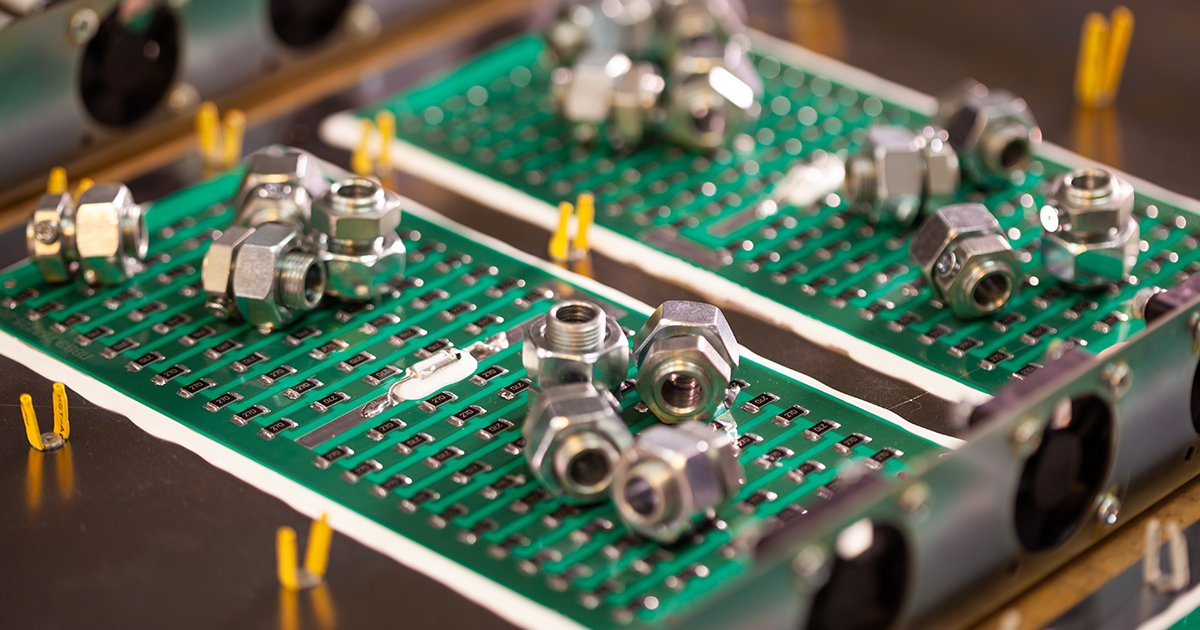
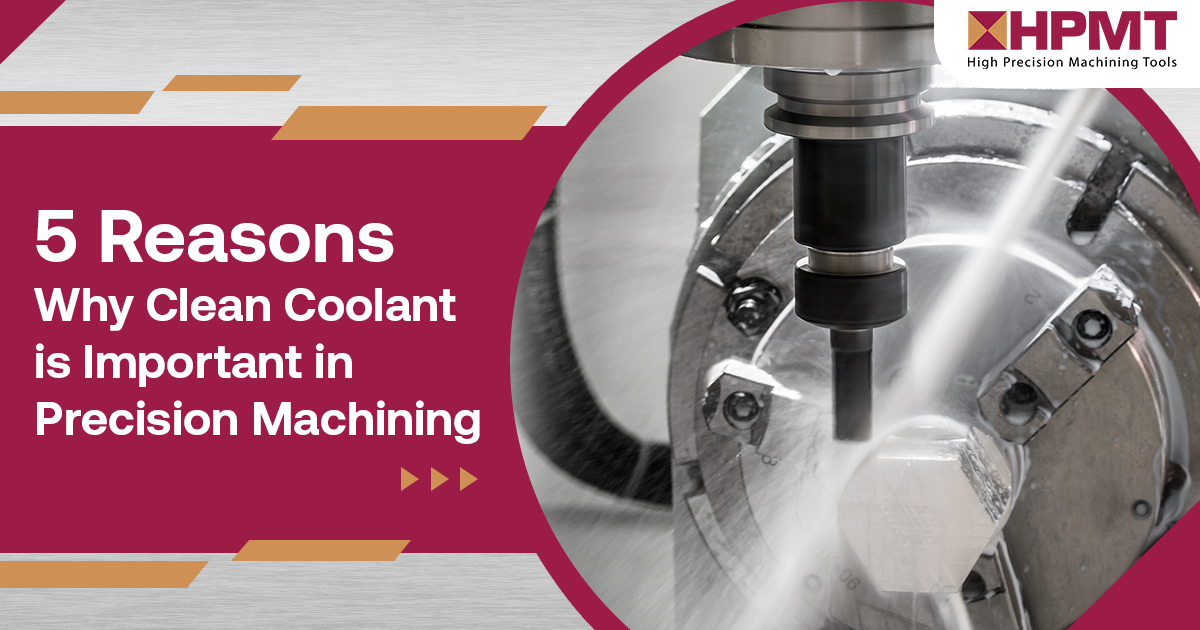
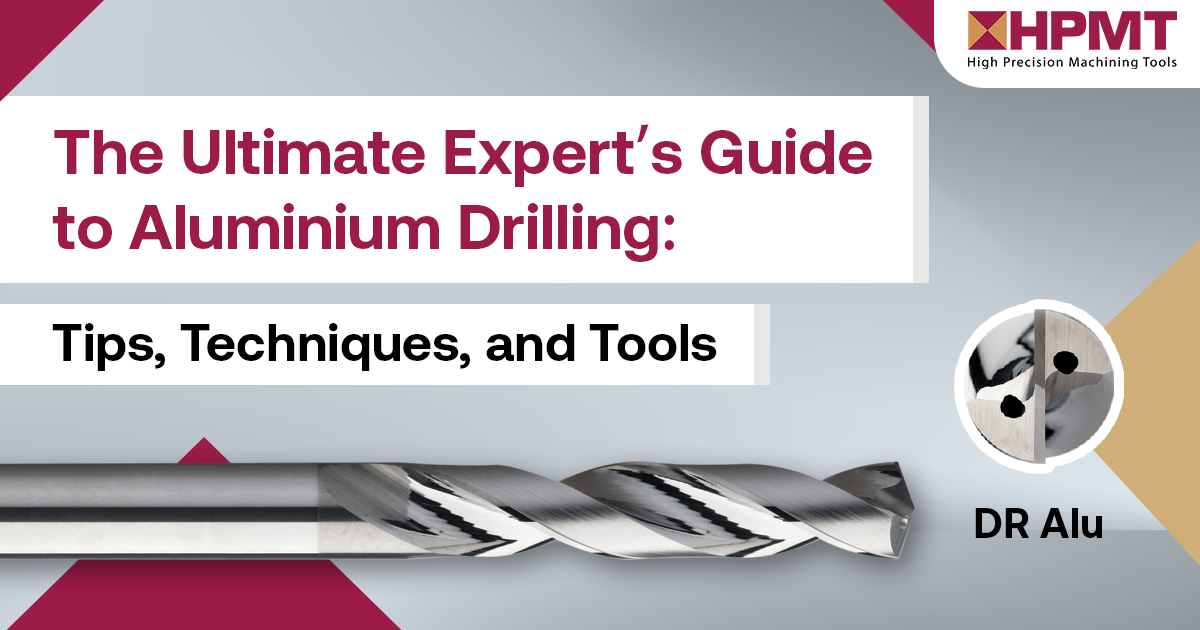