CNC End Milling 101: A Beginner's Guide

What is CNC End Milling?
CNC end mills are cutting tools used in milling machines to remove material from a workpiece. They are used for making shapes and holes during applications such as milling, profiling, and contouring. End mills have cutting teeth positioned on the face and edge of the body and can cut various materials in multiple directions.
This beginner's guide will cover the fundamentals of CNC end milling, including end mill shapes, flutes, other details, and coatings. By the end of this guide, you'll understand the different types of end mills and how to select the right one for your CNC machining needs.
End Mill Type
When it comes to CNC end milling, the type of end mill used is an essential aspect that can greatly impact the cutting capabilities and resulting workpiece quality. HPMT, a leading cutting tool manufacturer, offers a wide range of end mill types to suit different machining needs, including square, ball nose, corner radius, and drills, each with unique benefits and applications.
Let's take a closer look at some of the most common end mill types and their applications:
End Mill Flutes
End mill flutes are the cutting edges on the end mill that affect material removal, surface finish, and chip evacuation. Fewer flutes provide more chip space and are suitable for softer materials, while more flutes increase tool strength and may reduce chip flow. Understanding the impact of flute number helps in selecting the correct and suitable end mill.
Below are the end mill flute types, along with their descriptions and ideal applications:
List of Services
-
2 Flutes End MillsList Item 1
Provides a good balance between chip clearance and tool rigidity.
Ideal for: Soft metals, such as aluminum and brass
-
3 Flutes End MillsList Item 2
Offers a balanced compromise between chip clearance, tool rigidity, and surface finish.
Ideal for: General-purpose milling of most materials
-
4 Flutes End MillsList Item 3
Provides a smoother surface finish and improved chip evacuation compared to 2 or 3-flute end mills.
Ideal for: Most milling operations, including roughing and finishing of flat surfaces, slots, and pockets
-
5 Flutes End MillsList Item 4
Provides improved surface finish and reduced tool deflection for deep pocketing and slotting operations.
Ideal for: High-speed machining of non-ferrous materials, such as aluminum and copper alloys
-
Multi Flutes (5 and more flutes) End Mills
Offers excellent surface finish, chip evacuation, and reduced deflection, making it ideal for high-speed machining.
Ideal for: Finishing operations, such as 3D contouring and profiling, on harder materials.
Detail of the End Mill
Choosing the right end mill for a machining project involves considering the diameter, length of the cut, and shank diameter. The diameter determines the width of the cut, the length of the cut determines the maximum depth of the cut, and the shank diameter should match the milling machine's chuck or collet size. These details determine the milling machine, ensuring optimal perfomance and quality in the machining process.
HPMT offers cutting parameter features that can help you determine the optimal settings for your tools based on the material and machining conditions. By using these features, you can ensure that you are using the right speed and feed rates, which will help to prolong the life of your cutting tools and achieve optimal machining performance.
End Mill Coatings
End mill coatings are used to improve tool life and performance. Some common coatings include titanium nitride, diamond-like carbon, and aluminum titanium nitride. Each coating offers specific benefits in terms of wear resistance, lubricity, and cutting speed.
End Mill Coating | Benefits |
---|---|
Titanium Nitride | Provides high wear resistance and is ideal for machining abrasive materials. |
Titanium Nitride | Offers excellent hardness and low friction, resulting in improved tool life and reduced heat buildup. |
Aluminium Titanium Nitride | Combines the benefits of both titanium nitride and aluminum oxide coatings, providing high wear resistance and improved surface finish. |
To sum up, CNC end milling plays a critical role in the manufacturing industry, and selecting the right end mill is vital for achieving accurate and efficient cuts. Knowing the various end mill shapes, flutes, details, and coatings is crucial in making informed decisions when choosing end mills for your CNC machining projects. By doing so, you can ensure that your end mills are optimized for your specific application, resulting in high-quality machining results.
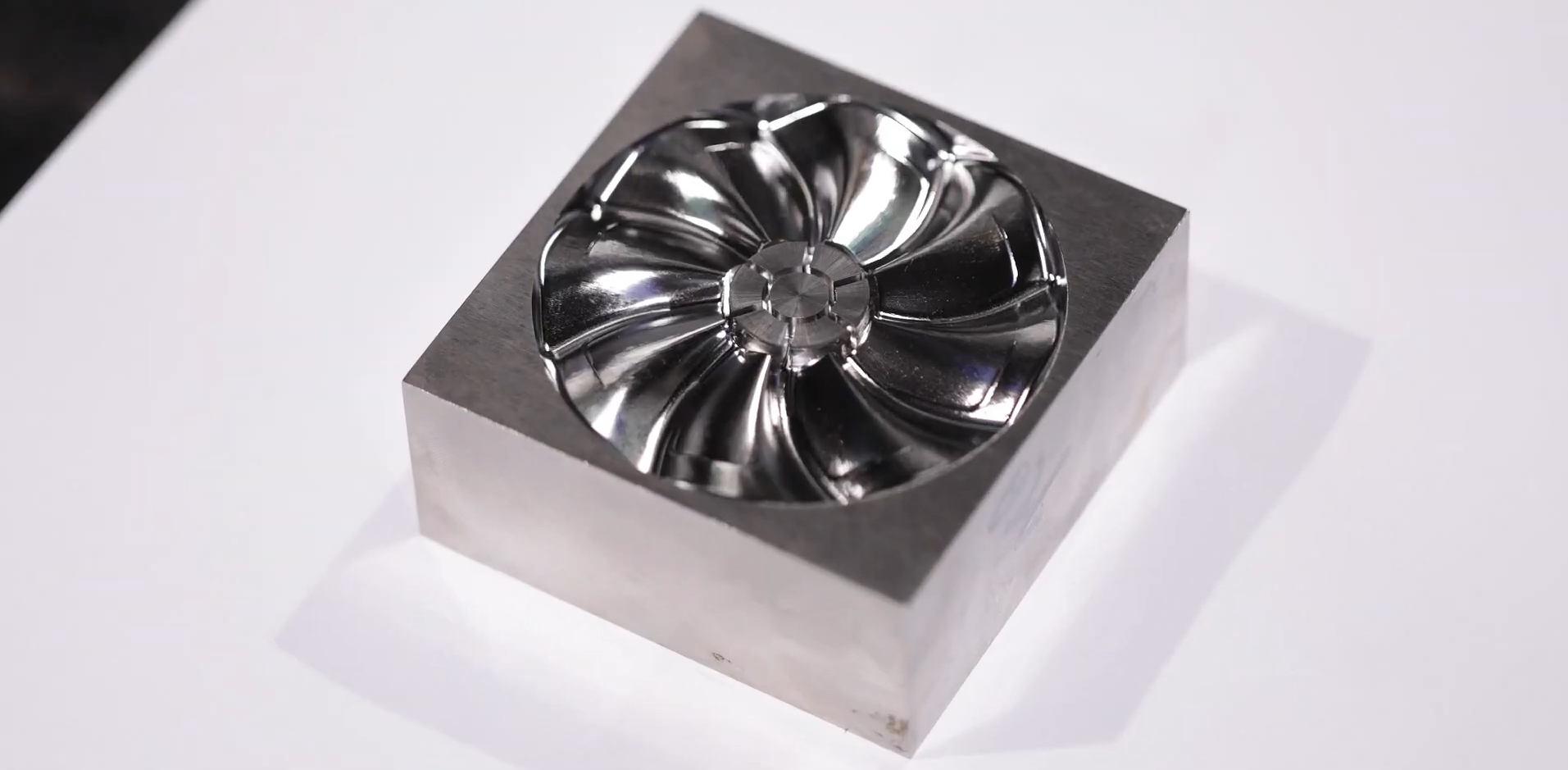
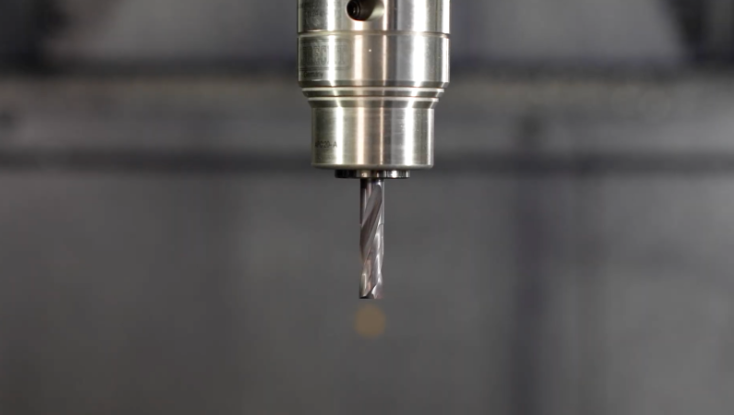
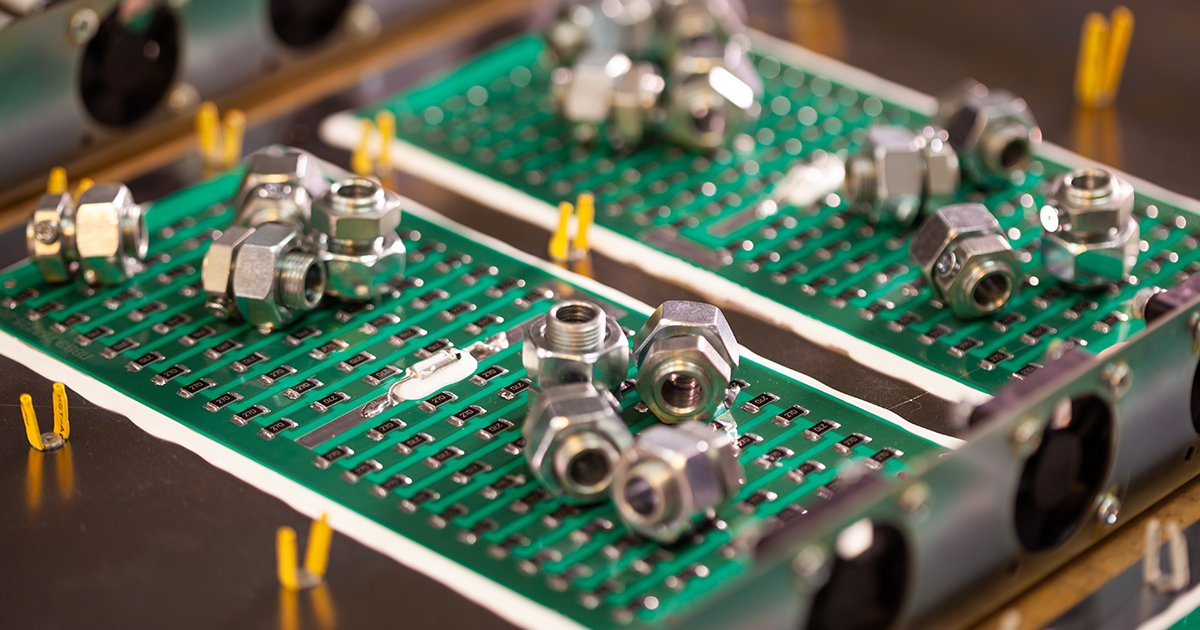
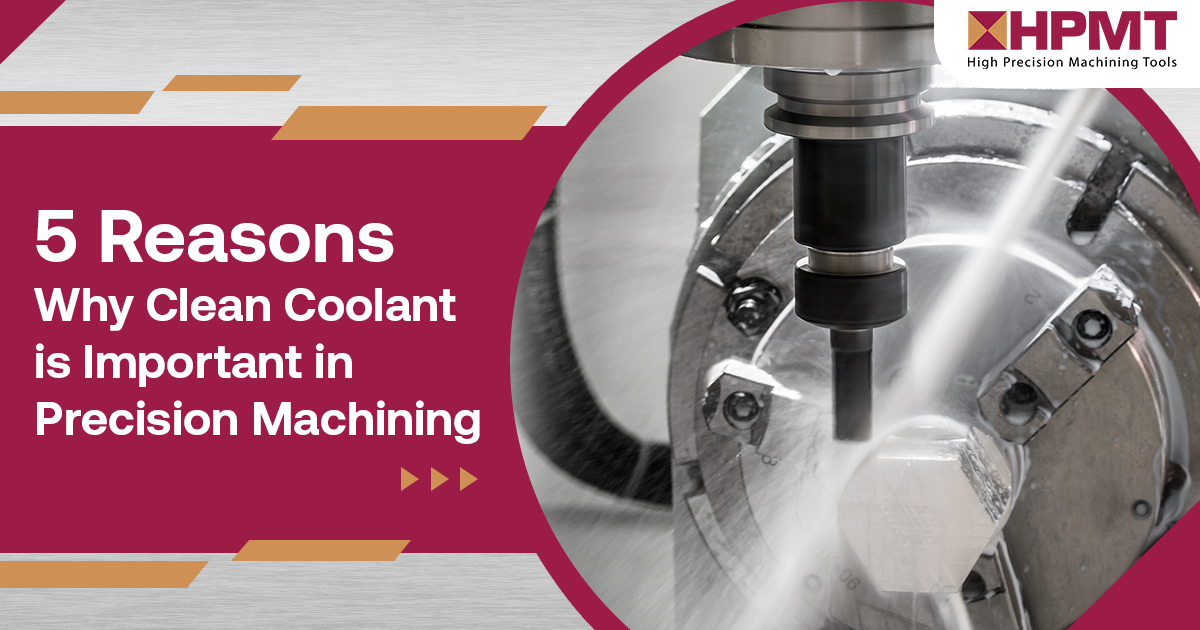
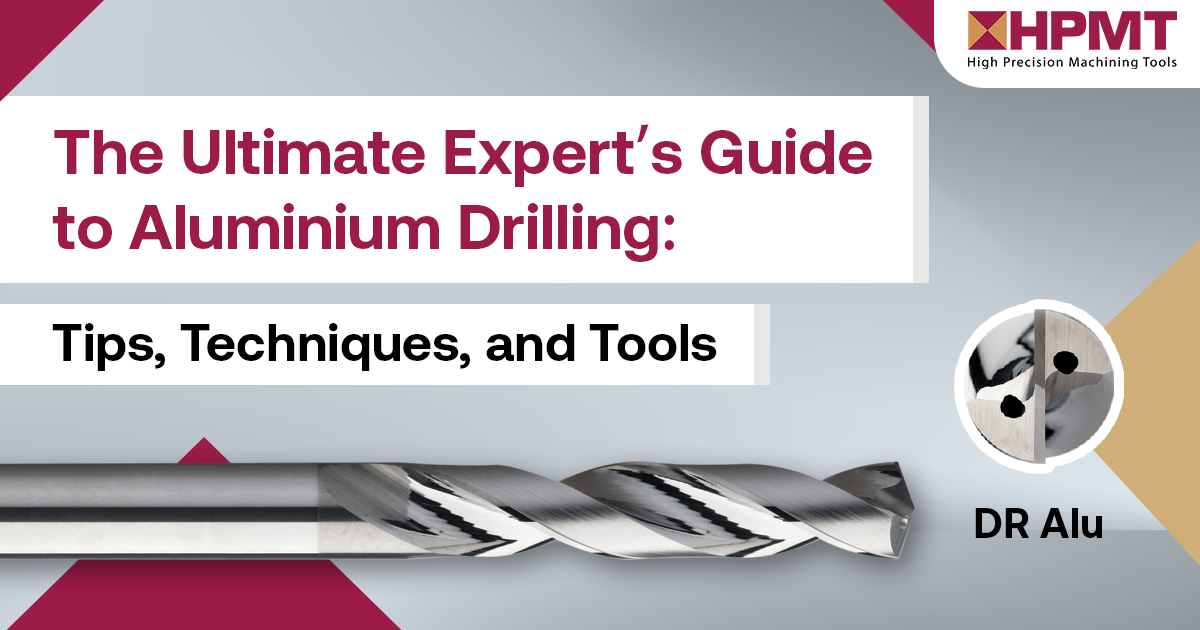